A operação eficiente de ativos industriais exige mais do que intervenções técnicas pontuais requer um sistema de gestão estruturado, baseado em dados, padronização de processos e decisões antecipadas. Nesse contexto, o PCM (Planejamento e Controle de Manutenção) emerge como uma função estratégica dentro da engenharia de manutenção, voltada para aumentar a confiabilidade operacional e garantir o melhor desempenho possível dos ativos físicos.
Com a crescente demanda por produtividade, competitividade e disponibilidade dos equipamentos, as organizações precisam ir além da abordagem corretiva e adotar metodologias que permitam planejar, priorizar e controlar as ações de manutenção com maior precisão. O PCM é o elo entre a gestão de ativos e a execução em campo, possibilitando uma visão integrada do ciclo de vida dos equipamentos e orientando a atuação técnica com base em indicadores de desempenho e criticidade.
Mais do que uma área de apoio, o PCM representa a inteligência operacional da manutenção capaz de transformar dados em ações concretas e resultados sustentáveis.
Neste artigo, você encontrará uma visão técnica aprofundada sobre o que é o PCM, quais os seus pilares, benefícios e como implementá-lo com excelência em ambientes industriais complexos.
Planejamento e Controle da Manutenção
O PCM (Planejamento e Controle da Manutenção) é um processo sistemático que visa planejar, organizar e monitorar as atividades de manutenção de forma tática e estruturada. Seu objetivo é reduzir falhas, evitar paradas não programadas e otimizar o uso dos recursos disponíveis (mão de obra, peças, tempo).
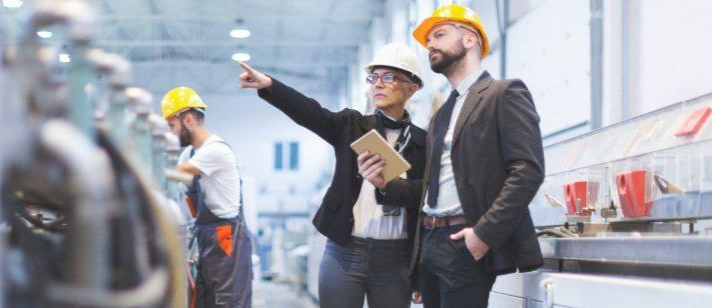
O PCM também é responsável por consolidar o histórico dos ativos e gerar informações confiáveis para a tomada de decisões, integrando-se à gestão de ativos da empresa. A atuação eficaz do analista de PCM depende do uso de dados como:
- Tempo médio entre falhas (MTBF)
- Tempo médio de reparo (MTTR)
- Criticidade dos ativos
- Backlog de manutenção
- Capacidade efetiva da equipe técnica
Objetivos do PCM
O Planejamento e Controle de Manutenção tem como foco principal:
- Redução de falhas e perdas de produção
- Aumento da confiabilidade e disponibilidade dos ativos
- Melhoria da eficiência operacional
- Otimização do uso de recursos técnicos e financeiros
- Redução do tempo de inatividade (downtime)
Além disso, o PCM fortalece a cultura de manutenção preventiva e preditiva, reduzindo a dependência da manutenção corretiva emergencial e, consequentemente, os custos associados.
Pilares do PCM: Pessoas, Processos e Ativos
A efetividade do PCM depende do equilíbrio entre três pilares fundamentais:
Pilar | Descrição |
Pessoas | Profissionais capacitados, motivados e alocados de forma estratégica. |
Processos | Procedimentos bem definidos, planos de manutenção estruturados e padronização. |
Ativos | Classificação por criticidade, histórico técnico e plano de manutenção adequado. |
Investir nesses três eixos garante melhor gestão da equipe, do orçamento, dos estoques de peças e integração entre os setores operacionais da empresa.
Por que o PCM é essencial para a indústria?
Confira os principais benefícios operacionais e estratégicos do PCM:
- Redução de falhas funcionais: a atuação proativa permite a antecipação de falhas e evita paradas críticas.
- Maior eficiência dos equipamentos: equipamentos operam em sua máxima eficiência (OEE) quando mantidos conforme especificações técnicas.
- Aumento da produtividade: a programação correta das intervenções evita paradas inesperadas no processo produtivo.
- Redução de perdas de produção: menos interrupções significa maior estabilidade na linha de produção.
- Redução de custos de manutenção: ações planejadas diminuem compras emergenciais, retrabalhos e perdas de materiais.
- Confiabilidade e disponibilidade ampliadas: equipamentos bem mantidos operam mais tempo com menos falhas.
- Diminuição do downtime: redução significativa no tempo de máquina parada.
- Aumento da qualidade dos produtos: equipamentos estáveis garantem conformidade com padrões de qualidade.
- Segurança e saúde ocupacional: redução de riscos operacionais por meio de ações planejadas e procedimentos seguros.
- Menor índice de retrabalho: intervenções bem planejadas e executadas corretamente na primeira vez.
Como implementar o PCM: etapas fundamentais
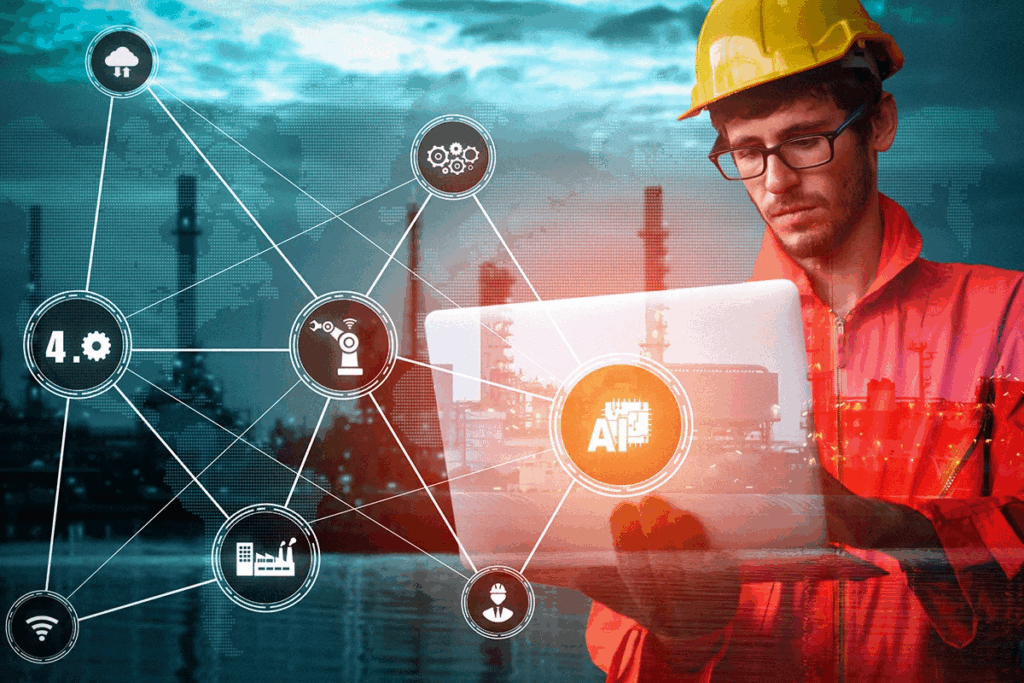
- Levantamento do histórico de manutenção dos ativos
- Análise crítica dos dados técnicos disponíveis
- Definição das tarefas por tipo de manutenção
- Elaboração do cronograma de manutenção
- Execução das ordens planejadas
- Monitoramento das ações e análise de resultados
- Revisão contínua dos planos com base nos indicadores
Tipos de manutenção no contexto do PCM
Tipo | Descrição |
Preventiva | Baseada em tempo ou uso; executada de forma periódica. |
Preditiva | Baseada em condição; monitora sinais de falha com sensores e inspeções técnicas. |
Corretiva planejada | Executada após falha esperada, em ativos de baixa criticidade. |
Detectiva | Identifica falhas ocultas sem interromper a operação. |
Produtiva Total (TPM) | Envolve operadores na manutenção; promove cultura de zero falha e zero acidente. |
Prescritiva | Baseada em dados, IA e algoritmos de previsão, estratégia da Manutenção 4.0. |
Desafios e maturidade do PCM
No Brasil, ainda é comum associar manutenção apenas a consertos. A implementação eficaz do PCM requer uma mudança de cultura e mindset por parte dos gestores. Isso passa por:
- Documentação técnica consistente
- Padronização de processos
- Adoção de tecnologias de monitoramento
- Gestão de indicadores em tempo real
Indicadores de desempenho para PCM
Monitorar a performance da manutenção é essencial. Os principais KPIs incluem:
- Disponibilidade dos equipamentos (%)
- Confiabilidade (nº de falhas evitadas)
- MTBF (Mean Time Between Failures)
- MTTR (Mean Time To Repair)
- OEE (Overall Equipment Effectiveness)
- Backlog técnico
- Tempo médio de atendimento de O.S.
Tecnologia no PCM: software de gestão
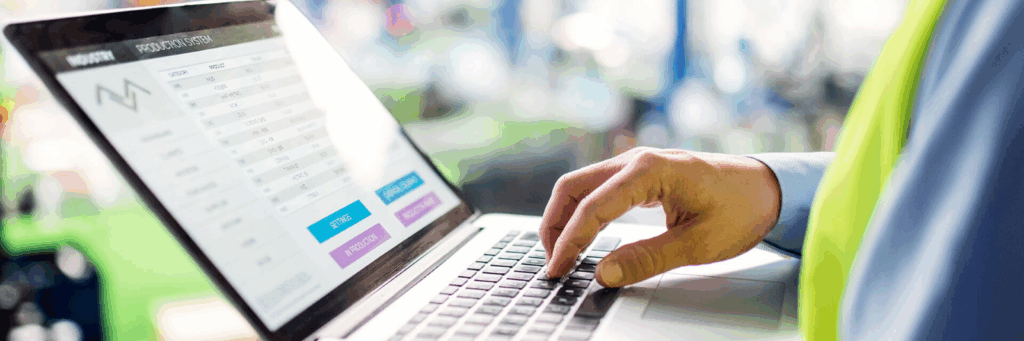
O uso de sistemas informatizados (CMMS ou EAM) melhora significativamente o desempenho do PCM. Entre as funcionalidades mais importantes estão:
- Planejamento e programação de ordens
- Gestão de estoque de peças
- Registro histórico técnico
- Integração com ERP e sistemas produtivos
- Geração de relatórios e indicadores
Dica: ao escolher uma solução digital, considere fatores como interface, suporte, escalabilidade e capacidade analítica.
Conclusão
O PCM é um componente crítico da engenharia de manutenção moderna. Quando estruturado de forma estratégica e sustentado por dados, processos e tecnologia, ele promove ganhos reais em disponibilidade, confiabilidade e redução de custos operacionais, fortalecendo a competitividade das indústrias diante de ambientes cada vez mais exigentes.
Investir em Planejamento e Controle de Manutenção não é apenas uma boa prática: é uma necessidade para quem busca desempenho consistente e gestão eficiente do ciclo de vida dos ativos.
Quer estruturar um PCM eficiente e orientado por dados na sua planta industrial?
Fale agora com um especialista da Sigma Gerenciamento de Projetos e descubra como transformar a sua manutenção em um diferencial competitivo.